[authors: Walker Prentke & Arthur Clarke]
The Expanding Sources and Costs of PFAS Contamination
Per- and polyfluoroalkyl substances (PFAS) investigation and litigation in the last few years has predominantly been focused on impacts which ultimately originate from the use, storage, and discharge of Aqueous Film Forming Foam (AFFF). Both 3M and Dupont have reached settlements in the multi district litigation bought by water supply companies, but there are doubts about whether the settlement amounts will be enough to cover capital costs for water systems as well as future O&M costs associated with the sophisticated technology needed to filter and remove PFAS from drinking water supplies.
For water suppliers there is then a question of where else they can recover the funds necessary for compliance. PFAS have been used for numerous years in consumer products. Beyond the spillages and releases associated with the manufacturing processes, these articles, once in the stream of commerce and then particularly at the end-of-life phase, can be environmental sources of PFAS. A singular product is likely to be a small source, but cumulatively, products can be large scale sources.
This article will discuss the technical aspects of fluorinated textiles, why they are used, and what the exposure routes to the environment are, which will provide insight into potential liability exposures related to these products. The following information may be of particular interest to attorneys in the product liability and environmental practice areas, as well as corporate counsel and environmental insurance underwriters.
PFAS Uses in Water and Stain-Resistant Clothing
PFAS in apparel have primarily been used in “high performance” apparel in which resistance to water, and in some cases oils—often marketed as “stain resistant”—has been desired. The principle under which these chemicals have been used are associated with the surface properties of materials.
How Fabrics Repel Water and Stains
Surface tension is a phenomenon defined by the United States Geological Survey (USGS) as “the property of a liquid that allows it to resist an external force due to the cohesive nature of its molecules.” Essentially, this is describing the fact that liquids have a bulk property and a surface property. Casual observances related to surface tension are easily apparent, particularly with insects that can “float on water” as shown in Figure 1.
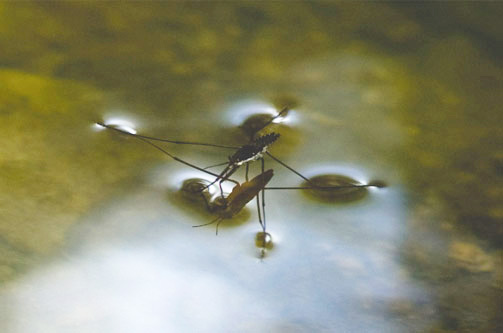
Figure 1 - Insect able to run freely on water surface due to the high surface tension of water.
Water is ubiquitous in human life but in many ways has unique properties. Water has a high surface tension due to its polarity and extensive hydrogen bonding. Because of this water can exert a high surface tension, since the mutual, cohesive attraction between water molecules is strong, and, therefore, a large amount of energy is needed to overcome these cohesive forces. A conceptualization of water molecules and water-oil interaction at the surface is shown below as Figure 2.
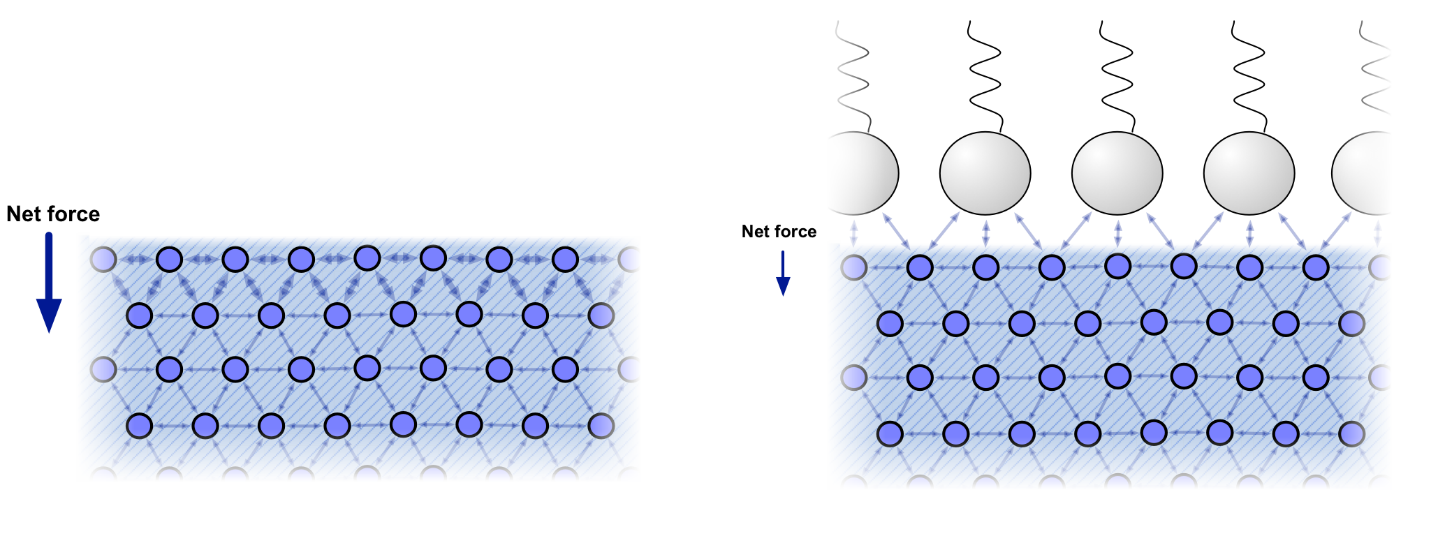
Figure 2 - Illustration of water molecules demonstrating cohesive intra-molecular bonding, and the conceptualization of these forces in response to the addition of an oil (https://errantscience.com/blog/2013/07/24/water-surface-tension/).
Textiles and apparel are solids, and, hence, the water resistance is a function of the solid-liquid interaction that occurs as either water or any liquid (“the stain”) is introduced to the surface. The theory of repellency is often defined as a condition of limited wettability (Kissa 2001), in which a treated fabric/textile is able to withstand penetration of a liquid under static conditions with no external forces being applied.
For a simple conceptualization of this phenomenon, imagine two distinct forces: a cohesive force of the liquid which holds the liquid together and the adhesive force of the interface between the solid and the liquid. Both can be measured using a metric unit known as the Dyne, which is equivalent to one gram per centimeter per second squared, or, in SI units, 10-5 newtons.
Water has a high surface tension measured at 72 dyne/cm at 25oC. Oils have a much lower value of approximately 20 to 31 dyne/cm. Conceptually, then, in order to make a surface impervious to both oils and water, the textile will require a low surface energy of below 20 dynes/cm. Traditional waterproofing agents like paraffin wax, when applied to a textile, can only achieve a surface energy of approximately 30 dynes/cm, which, while conferring water resistance, would not provide oil resistance (oleophobicity).
The need for low energy surfaces in these high-performance textiles is what drove the uptake and application of fluorinated compounds to treat textile surfaces. These compounds can reduce the surface energy of a treated surface to as low as 15 dynes/cm, below the surface tension of both oils and water. When applied to the treated textile, the liquid is thereafter said to not be wettable on the surface, meaning that the cohesive forces of the liquid are maintained, and there is no ability of the liquid to spread and penetrate the surface as illustrated below in Figure 3.
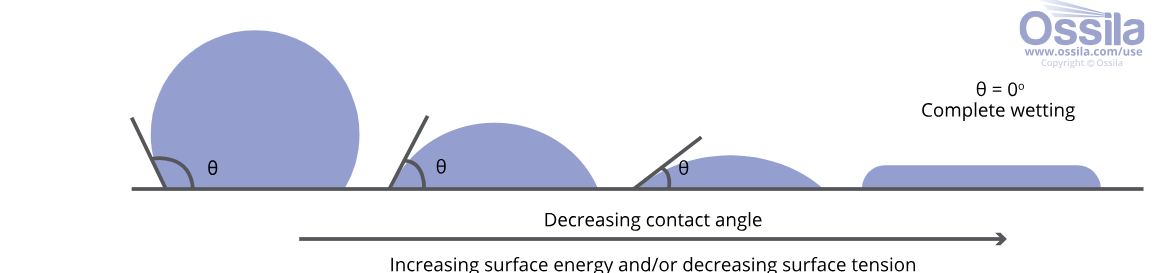
Figure 3 – Graphical illustration of wetting of a liquid drop on a surface ( https://www.ossila.com/pages/a-guide-to-surface-energy).
How Fluorinated Polymers Made Water-Resistant Fabrics More Durable
Many people are familiar with PFAS compounds such as perfluorooctanoic acid (PFOA) and perfluorooctanesulfonic acid (PFOS), which were common components or breakdown products of compounds used in aqueous film forming foam (AFFF). While these compounds can impart low energy surface properties, they were not optimized to be used as coatings in their native state. This is because they are highly water soluble, and, as such, a treated textile would experience rapid loss of functionality after going through repeated laundry wash cycles. This spurred the need for a system in which the low energy surface could be delivered and thereafter remain stable on the surface of the fabric with minimal loss of function through wash cycles.
It was this need that spurred the use of polymer-based solutions for coating textiles. The polymer can be applied to the textile and then cured (i.e., baked at relatively low temperatures) to form a stable outer lining, while providing the textile with a low surface energy which imparts water and stain repellency. Generally, a class of polymers known as side-chain fluorinated polymers have been the primary class of compounds used for this purpose.
Side-Chain Fluorinated Polymers (SCFP) and Their Role in Fabric Coatings
Arguably the world’s most famous fluoropolymer is polytetrafluoroethene (PTFE), often known by the trade name TEFLON. This polymer contains a carbon backbone with fluorine atoms directly attached to the backbone as demonstrated below in Figure 4.
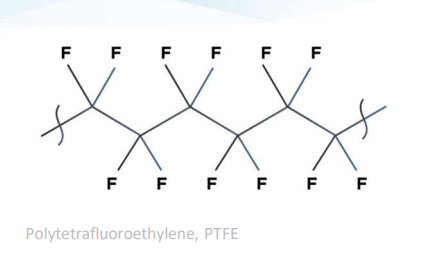
Figure 4 - PTFE structure (Plastics Europe).
Side-chain fluoropolymers (SCFP), by contrast, have a hydrocarbon polymer backbone, with fluorinated side-chains extending off the backbone, sometimes interceded by other hydrocarbon side-chains, as demonstrated below in Figure 5.
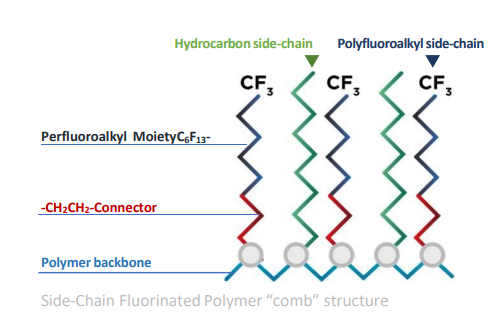
Figure 5 Fluorinated side-chain polymer (Plastics Europe).
SCFPs have active surface properties, particularly with respect to PTFE which is favored more for its bulk, or material properties.
The most common form of these SCHPs is based on acrylate or urethane polymer backbones, which generally act as the bonding agent to the fabric and extend the performance range of the perfluorinated side-chains (Franchina 2002). Historically, prior to the voluntary phase out of long-chain PFAS initiated by the USEPA in 2002, side-chains included C8 compounds such as PFOA and PFOS and/or their precursors. To provide an example of scale, reporting by 3M in 2000 indicated that around 2400 tons of perfluorooctylsulfonyl fluoride (POSF, a precursor to PFOS) was used to made SCFP, in comparison to around 150 tons that year that was used to manufacture AFFF. Data collected by the USEPA in 2006 indicated that a combined 7200 tons of PFAS were manufactured by DuPont, Asahi, Clariant, and Daikin for use in SCHPs.
Following the phase-out of long-chain PFAS in 2002, the newer generation of SCFP manufactured in Japan, Europe, and the US were generally based around either C6 or C4 PFAS, with some longer chain compounds still being manufactured and sold by Chinese firms. Generically, 3M appears to have adopted the C4 perfluoro sulfonic acid PFBS as their preferred side-chain, while “telomer” PFAS manufacturers generally used C6 fluorotelomer alcohols as their side-chains.
Potential Release Pathways of PFAS from Fluorinated Textiles and Their Environmental Impact
Potential releases from fluorinated textiles can be summarized as follows:
- Direct release to the environment, and potentially the wearer, during common use.
- Releases during the washing cycle.
- End-of-life releases arising from disposal of the textiles.
The emissions from direct contact and use of textiles articles are likely to be low. Releases during the wash cycle have been subject to a small number of studies, all of which have indicated that there are discharges from the washing process. The discharges have been quantified as microscopic discharges of fluorinated textiles. The microfibers are released during the wash cycle, and from there they are expected to enter the environment. Fibers from the washing process can be discharged into sewers. At this point, some of the fluorinated side-chains may be hydrolyzed from the polymer backbone and become mobile in the water supply. Solid fluorinated fibers will be filtered out at water treatment centers. If the treatment center has participated in the sale of bio solids for use as fertilizer, the fluorinated fibers can potentially be spread over agricultural land as applied bio solids, with PFAS likely to be slowly released at this point. This scenario, along with estimated loadings from C6 (perfluorohexanoic acid, or PFHxA) treated polyamide fabrics (aka, Nylon) is shown below in Figure 6.
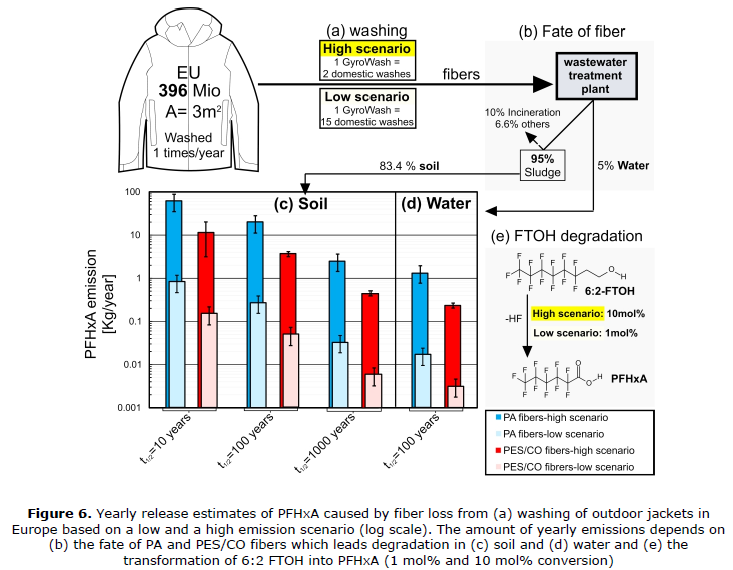
Figure 6 – Modelled PFAS releases from fluorinated Polyamide textiles in Europe (Schellenberger et al 2019).
Fluorinated textiles are also likely to be a significant source of PFAS in groundwater for years to come based on their disposal in landfills. There are two proposed mechanisms by which the SCFP can degrade and release PFAS in a landfill situation: hydrolysis of the fluorinated side-chain or breakage of the carbon backbone, as illustrated below in Figure 7.
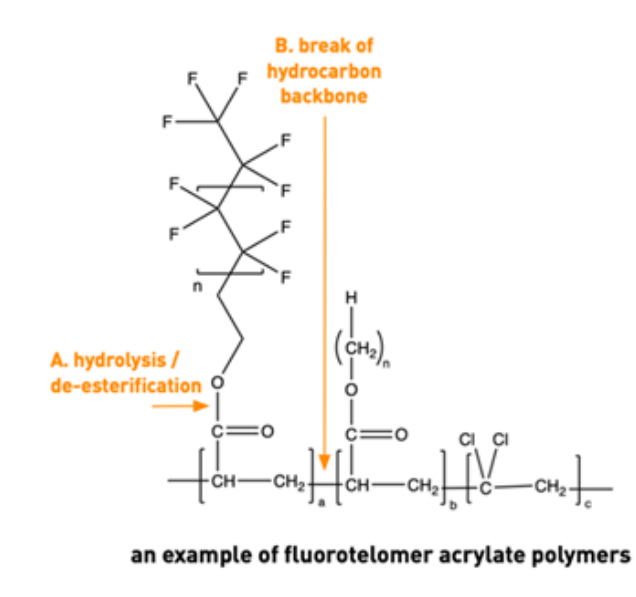
Figure 7 - Mechanisms of release of fluorinated chains from a polymer backbone (OECD 2022).
The hydrolysis mechanism has been shown to occur in various studies, with half-lives differing depending on the conditions. Landfills offer a high heterogeneous set of environments under which there may be high variation in degradation waste. Once the PFAS has been leached out in the landfill, it has the potential to enter and travel in the environment by conventional means, i.e., through a leachate discharge from the landfill which does not treat PFAS, then into the wider environment.
Understanding Environemntal Liabilities Tied to Fluorinated textiles
Product liability for products with fluorinated coatings—in this example, textiles—offer a much wider scale of potential product liabilities which may extend to environmental liabilities. Unlike asbestos or talc which had discreet exposure routes, the potential for PFAS contamination of environmental media and subsequent exposure arising from textiles is vast. Public water utilities and providers who are required to comply with extremely low drinking water limits may seek further cost recovery for capital expenditures and operation expenses from companies who introduced PFAS-containing textiles into the stream of commerce.
Many of these textiles were manufactured and coated overseas, particularly in South Asia, and as such there is limited liability related to the manufacturing process. However, clothing and apparel companies are likely to still retain liability for the release of PFAS from their products, and these items are likely to stay as sources to the environment, either through washing cycles or in landfills for possibly decades to come. This is conceptualized in Figure 8 below.
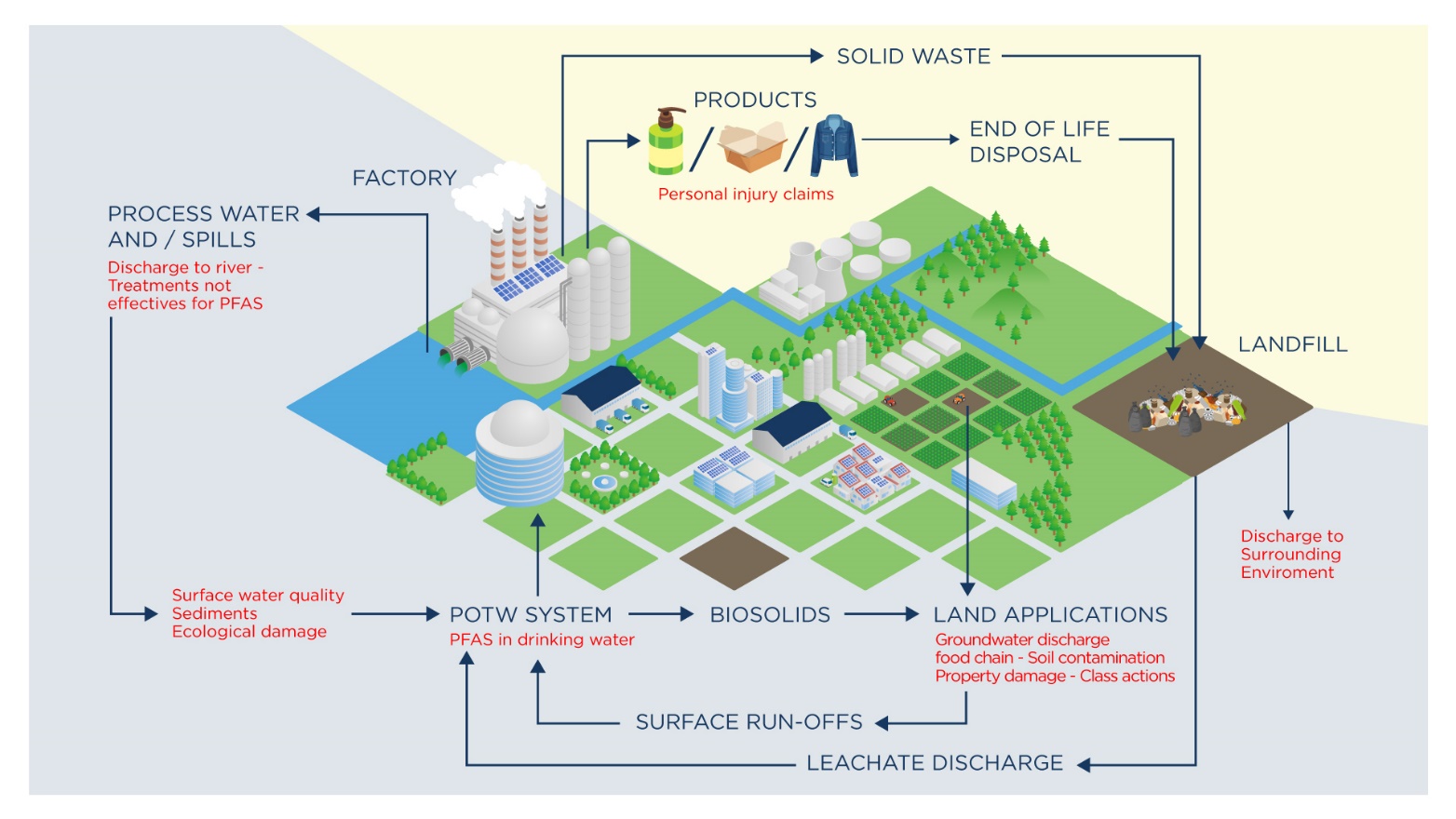
Figure 8 - Conceptualized liabilities arising from PFAS-containing textiles.
For potential claimants, there may be significant difficulty in establishing a direct nexus between PFAS in a public water system and a specific brand of clothing. There are, however, estimations and approximations that can reasonably infer how much total mass of PFAS a given set of textiles may release under certain conditions. Records showing performance certification for surface energy of textiles can generally be used to infer weather or not a textile was fluorinated based on the surface energy regardless of whether any direct evidence from an overseas manufacturing facility is available.
How States Are Regulating PFAS in Textiles
Several states have introduced legislation limiting PFAS content in textiles and other consumer products, including California, Colorado, Maine, Maryland, Minnesota, and, most recently, New Mexico. California’s ban contains compliance testing for textiles which need to be below 100ppm in a Total Organic Fluorine (TOF) test, reducing to 50 ppm in 2027. At the moment, state regulation and compliance must be undertaken on a state-by-state basis.
For organizations navigating these evolving standards, environmental due diligence and environmental investigation and remediation services experts offer support in understanding environmental exposures, managing risk, and maintaining regulatory compliance.
Acknowledgments
We would like to thank our colleagues Walker Prentke and Arthur J. Clarke, J.D., for providing insight and expertise that greatly assisted this research.
References
- Franchina, J.G., 2002. High-Durability, Low-Yellowing Repellent for Textiles (Google Patents).
- Steffen Schellenberger, Christina Johnsson, Pelle Mellin, Oscar Levenstam, Ioannis Liagkouridis, Anton Ribbenstedt, Ann-Charlotte Hanning, Lara Schultes, Merle Plassman, Caiza Persson, Ian Cousins and Jonathan Benskin, Release of side chain fluoropolymer containing microplastic fibers from functional textiles during washing and first estimate of perfluoro alkyl acid emissions. Environmental Sci. Technol 2019.
- OECD, 2022, Synthesis Report on Understanding side-chain Fluorinated Polymers and Their Life Cycle, OECD series on risk management No. 73, Environmental Health and Safety, Environmental Directorate, OECD.
- Erik Kissa, Fluorinated Surfactants and Repellents, Second Edition, Surfactant Science Series Volume 97, 2001.
- Plastics Europe, www.plasticseurope.org
- https://www.usgs.gov/special-topics/water-science-school/science/surface-tension-and-water#:~:text=Surface%20Tension%3A%20%22The%20property%20of,phenomenon%20known%20as%20surface%20tension.